WASSERAUFBEREITUNG AUF HÖCHSTEM NIVEAU
Die HS2-Baustelle des Bauloses West Ruislip im Westen Londons ist riesig. Der Ausblick vom Eindicker der Wasseraufbereitungsanlage (WWTP) verschafft einen Eindruck von den laufenden Aktivitäten. Kaum noch sichtbar von hier: das neue Portal des Northolt-Tunnels. Davor die riesigen Förderbänder, die den Abraum des Tunnelvortriebs abtransportieren. Weiter entfernt sieht man die Stapel vorgefertigter Tunnelsegmente, die in der Nacht per Bahn angeliefert werden.
Obwohl man es von hier aus nicht sehen kann, ist das mit dem Tunnelbau beauftragte Joint Venture Skanska Costain Strabag (SCS) auch oberirdisch aktiv. Im Rahmen der Lose S1 und S2 baut SCS Brücken und andere Bauwerke, die die Hochgeschwindigkeitsstrecke HS2 bis zu den in offener Bauweise entstehenden Tunneln tragen sollen, ab denen sie unterirdisch verläuft.
All diese Bauarbeiten bedeuten auch viel Arbeit für die Wasseraufbereitungsanlage. Zusätzlich zum Schmutzwasser der beiden EPB-Schilde muss die WWTP auch das Schmutzwasser der vielen Beton- und Wascharbeiten aufnehmen und wieder aufbereiten.
Die Kapazität der Anlage liegt bei 150 Kubikmetern pro Stunde. Eine weitere Anlage mit einer noch höheren Kapazität von 250 Kubikmetern pro Stunde wird im Laufe des Jahres in Betrieb genommen, wenn der Vortrieb der Querschläge zwischen den beiden Haupttunneln beginnt.
Der Großteil des Wassers, das die Anlage gereinigt verlässt, wird wiederverwendet und zurück in den Untergrund geleitet, um dort die TBM zu versorgen. Die WWTP muss zugleich in der Lage sein, das Wasser entsprechend den strengen Grenzwerten der britischen Umweltbehörde aufzubereiten, damit es im Fall von Überkapazitäten in die Themse eingeleitet werden kann.
„Die Vorschriften zur Wasserqualität werden in vielen Ländern zu Recht strenger“, sagt Gino Vogt, Leiter von Herrenknecht Separations, der uns über die Anlage führt. „Vor einigen Jahren hätte noch ein Absetzbecken auf der Baustelle genügt, aber jetzt sind Wasseraufbereitungsanlagen unabdingbar. Sie müssen flexibel und effizient sein, um eine Vielzahl von Parametern sowie Schadstoffen zu behandeln, je nachdem, was auf der Baustelle passiert und was im Boden ist.“
Dass TBM und WWTP von ein und demselben Lieferanten kommen, macht dem Tunnel- und Anlagenmanager Francesco Giampietro von SCS das Leben leichter. „Der Wegfall einer Schnittstelle hat Vorteile für uns“, erläutert Giampietro. „Es macht den Planungsprozess einfacher und bedeutet, dass wir bei der Dimensionierung und Installation der Anlage effizienter sein können.“

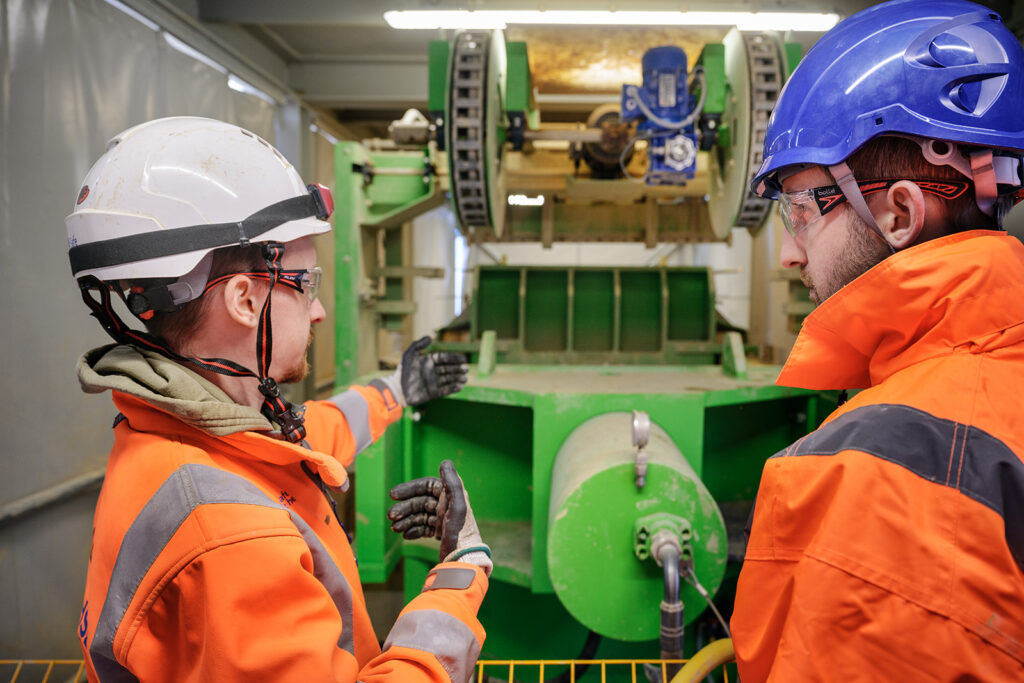
Dank ihrer Containerbauweise und des modularen Ansatzes kann die WWTP flexibel an die wechselnden Anforderungen auf der Baustelle angepasst werden.
Der Prozess zur Wasseraufbereitung beginnt auf dieser Baustelle mit drei riesigen, von SCS bereitgestellten Absetzbecken mit einem Fassungsvermögen von je circa 1.000 Kubikmetern, die aus der Ferne auch für rechteckige Schwimmbecken gehalten werden könnten. Sie dienen dazu, die Überproduktion zwischenzuspeichern und das Oberflächenwasser aufzufangen. Am Tag unseres Besuchs sind zwei der drei Becken leer und das Sediment wird gerade ausgehoben.
Das der WWTP nächstgelegene, dritte Becken ist in Betrieb. Von dort wird das Wasser in den Puffertank der Wasseraufbereitungsanlage geleitet. Parallel zu dieser Leitung verlaufen noch zwei weitere zur Anlage – eine von jeder der beiden TBM.
Der Puffertank fasst etwa 250 Kubikmeter und ist mit einem Rührwerk ausgestattet, das dafür sorgt, dass das Schmutzwasser homogen bleibt. Denn wenn die Konsistenz zu stark schwanken würde, müsste die Dosierung der Chemikalien im weiteren Verlauf des Aufbereitungsprozesses zu oft verändert werden. Das Ergebnis wäre inkonsistent. Sensoren im Tank messen die Trübung, den pH-Wert und die elektrische Leitfähigkeit des Schmutzwassers, um festzustellen, ob Metalle oder Salze vorhanden sind.
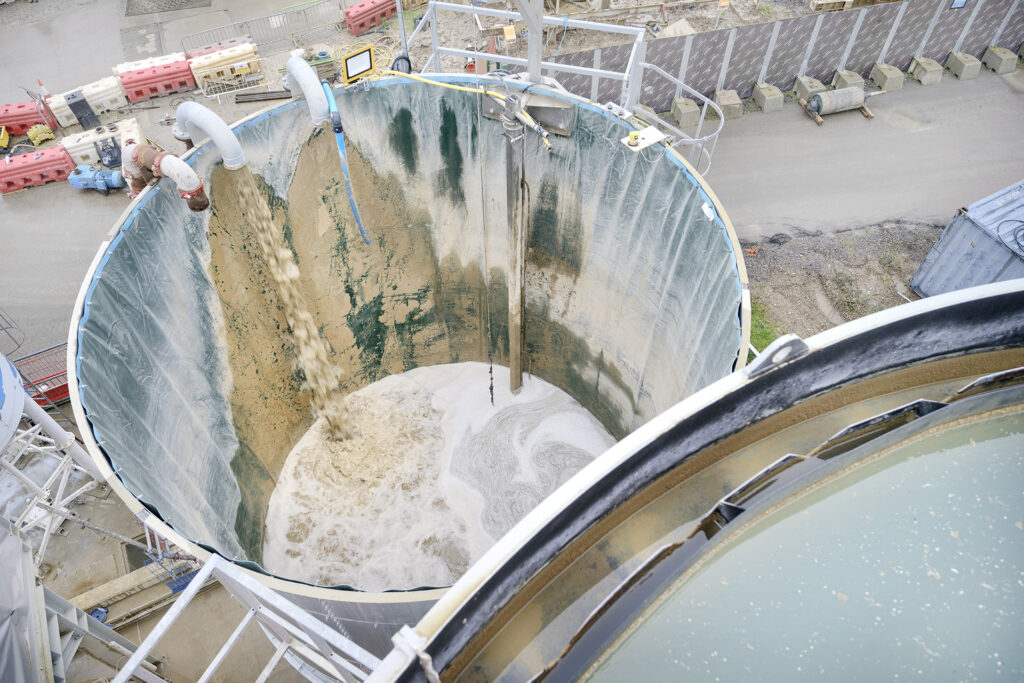
VIRTUELLE VORSCHAU
Anhand eines Displays, das den Prozess digital anzeigt, erklärt Keiton Wall, verantwortlicher Operator bei SCS, was er und seine Kollegen stets im Auge behalten: „Während das Wasser durchfließt, überprüfen wir zum Beispiel den pH-Wert. Wenn er nicht stimmt, zirkuliert das Wasser so lange weiter im Tank, bis es im Zielbereich ist. Wir achten auch auf die Trübung, da sie mehrere Prozessschritte wie beispielsweise die Filterpresse beeinflusst. Außerdem kontrollieren wir, ob das Wasser schnell genug durchläuft, da es sonst zu Verstopfungen kommen kann.“
An unserem Besuchstag enthält das Schmutzwasser im Eingang nur 0,539 Gramm Feststoffe pro Liter, ein niedriger Wert. Die WWTP ist in der Lage, bis zu 40 Gramm pro Liter zu verarbeiten. Am Ende des Prozesses befinden sich nur noch 10,02 Milligramm pro Liter im Wasser. Der beim Einlass sehr alkalische pH-Wert von 14 ist in der Zwischenzeit auf neutrale 7,5 beim Auslass gesunken.
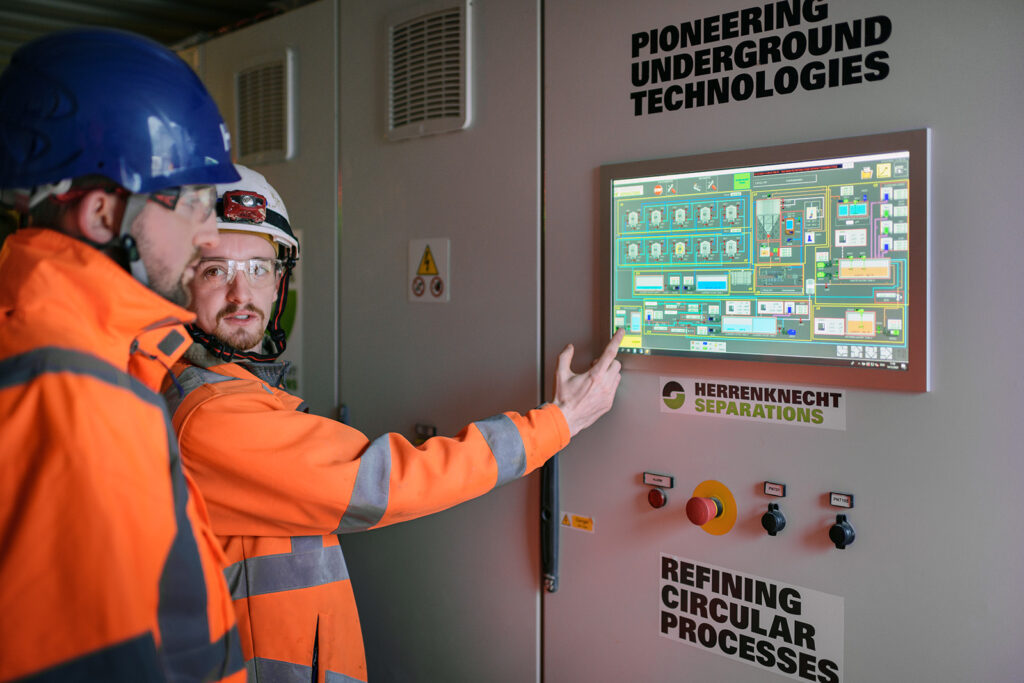
Wie fast alle Teile der Anlage ist auch der Steuerstand in einem Container untergebracht. Keiton Wall, einer von drei Technikern bei SCS, die hier arbeiten, gibt eine Führung.
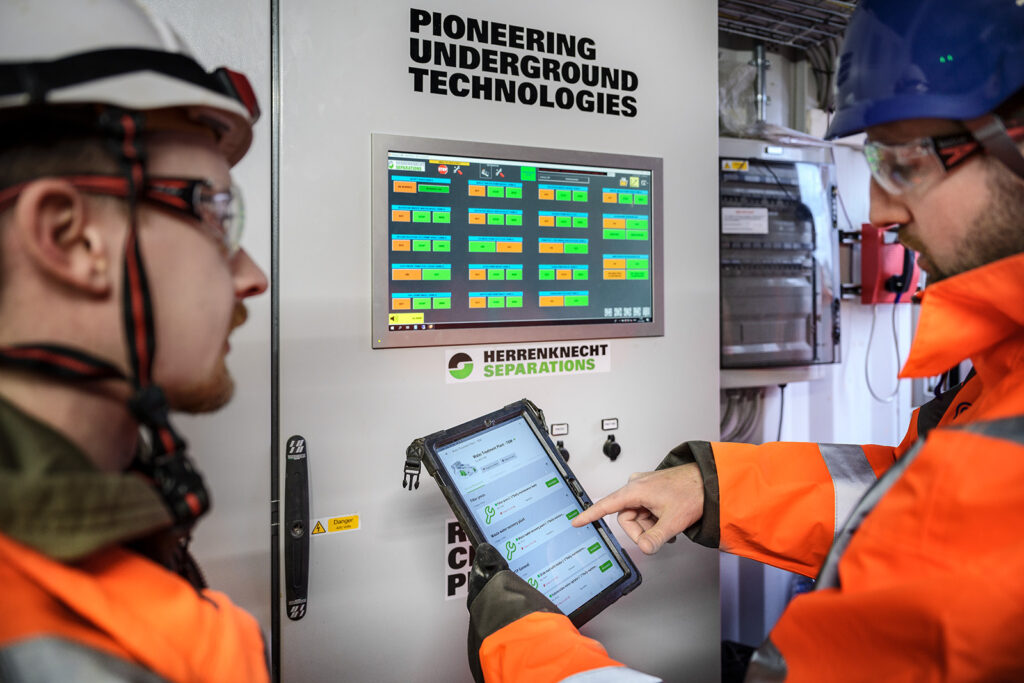
An den meisten Tagen müssen Wall und sein Kollege regelmäßige Kontrollen der Anlage durchführen. Das auf einem Tablet installierte Maintenance.ON-Modul erinnert sie daran.
FERNWARTUNG MIT DIGITALER PLATTFORM
Herrenknecht.Connected ist eine digitale Plattform, die Daten aus den TBM, WWTP und anderen Anlagen im Zuständigkeitsbereich von Herrenknecht sammelt, verwaltet und visualisiert. SCS nutzt Herrenknecht.Connected, um den Baufortschritt mit maßgeschneiderten Dashboards und Reports zu überwachen und die Stakeholder über das Geschehen auf der Baustelle auf dem Laufenden zu halten. Auch Anlagen, die nicht von Herrenknecht geliefert wurden, managt SCS bei diesem Projekt über das Maintenance.ON-Modul der Herrenknecht.Connected-Plattform.
Später am Tag führt Wall die vorgesehenen Aufgaben aus, meldet in der App, wenn sie erledigt sind, und fügt, wenn nötig, noch Fotos und Notizen hinzu. Die Daten speist er über ein Tablet in das System ein.
CHEMIKALIENCOCKTAIL
Vom Puffertank gelangt das Schmutzwasser in einen kleineren 10-Kubikmeter-Tank, in dem es mit einem Mix aus Chemikalien behandelt wird. Die Chemikalien variieren von Baustelle zu Baustelle und sogar während eines Projekts. Die Betonarbeiten in West Ruislip haben beispielsweise den Chromgehalt des Wassers über das erwartete Maß hinaus ansteigen lassen, sodass der Behandlungsprozess und die Chemikaliendosierung optimiert werden müssen.
„Weil Baustellen üblicherweise die Eingangswerte wegen wechselnder Arbeiten nicht garantieren können, müssen wir die Anlagen regelmäßig anpassen. Darum müssen wir und unsere Anlagen flexibel sein“, betont Vogt. „Durch unsere Containerbauweise und den modularen Ansatz lassen sich Elemente leicht hinzufügen und wir können via Fernwartungsmodul unterstützen.“
Unter den Chemikalien, die dem Wasser zugesetzt werden, befindet sich ein spezielles, vorher getestetes Flockungsmittel, das die feinen Schwebeteilchen im Wasser kumulieren lässt. Die Anlage passt die Dosiermenge durch Sensorik automatisch an den jeweiligen Bedarf des Schmutzwassers an.
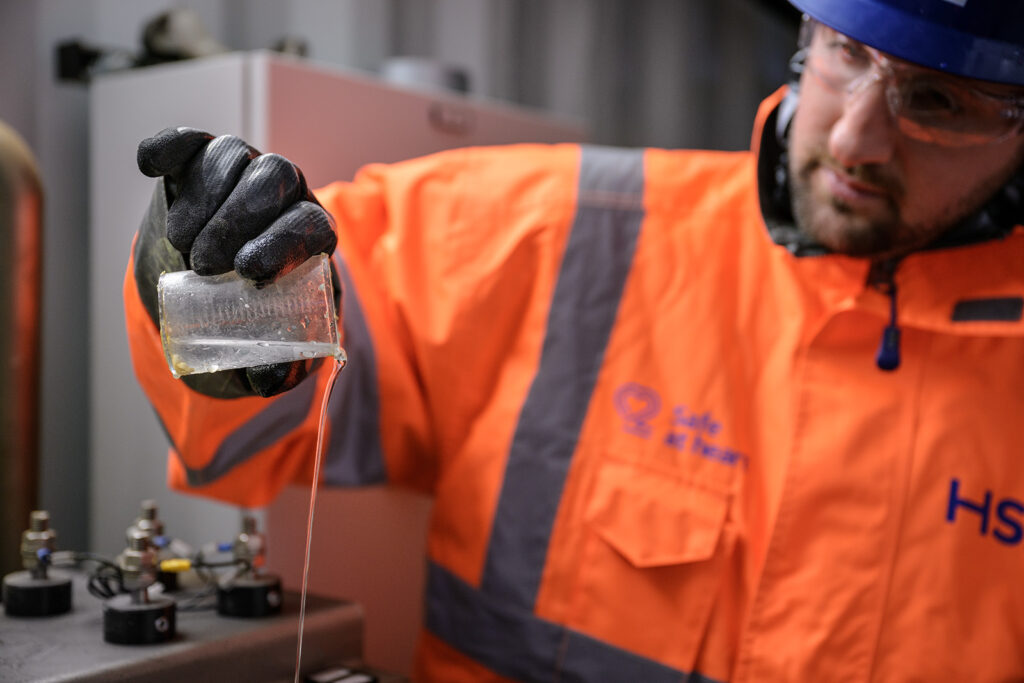
HERZ UND HIRN
Der zu Beginn erwähnte lineare Eindicker bietet mit seiner Zugangsleiter und einer Plattform am oberen Rand den Überblick über das Baustellengelände. Wer in den oberen Teil des Eindickers hineinblickt, sieht einen zentralen Trichter, der sich zum Boden des Behälters hin verjüngt.
Die Feststoffe, die mit dem Flockungsmittel reagiert haben, setzen sich im Trichter ab, während das saubere Wasser über den oberen Rand schwappt und weitergeleitet wird. Ein sich langsam bewegender Abscheider reinigt die Außenwände des Trichters und homogenisiert die Ablagerungen.
Im Inneren der Konstruktion, am Fuß des Eindickers, befindet sich das, was Vogt als das „Herz und Hirn“ der Anlage bezeichnet. Beim Hindurchgehen fällt der Blick auf einen gläsernen Behälter, der ein chemisches Experiment mit einer leuchtenden Röhre in der Mitte zu enthalten scheint: die „Floccmaster Control Station“.
Die Station misst die Effizienz und die Reaktion der Flockenbildung der Feststoffe im Schmutzwasser. Dazu führt sie einen optischen Sensor durch das Rohr und die darin enthaltene Flüssigkeit, während der Durchfluss für einige Sekunden gestoppt wird. „So bestimmen wir, ob das eingedickte Schmutzwasser mit gutem Ergebnis zur Filterpresse weitergeleitet werden kann oder ob es mit angepassten Parametern ein weiteres Mal mit Flockungsmittel behandelt werden muss“, erklärt Vogt.
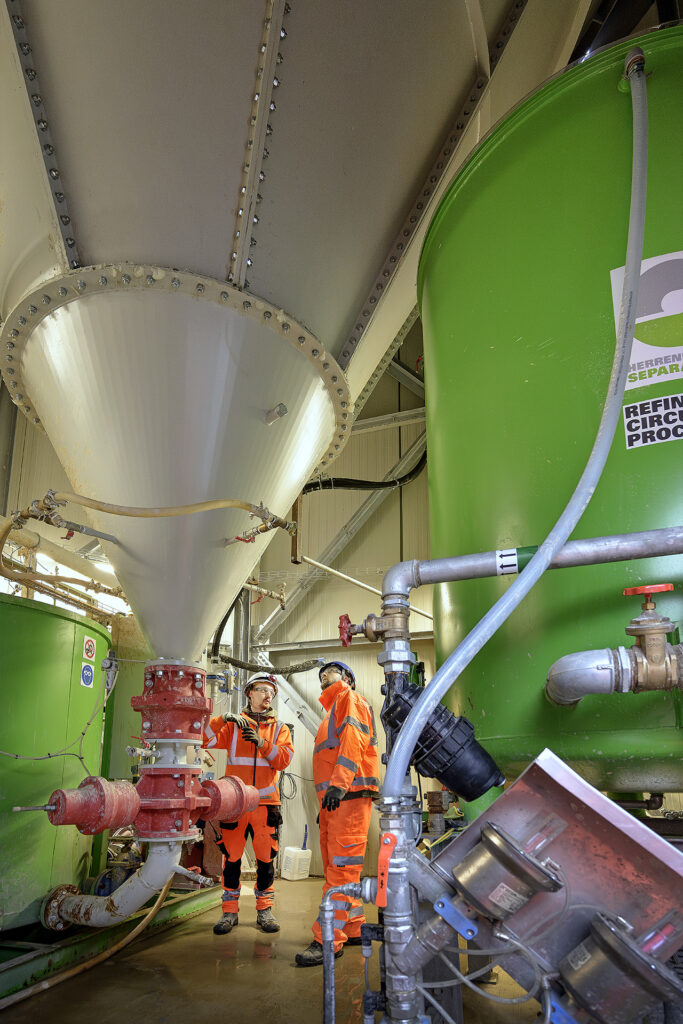
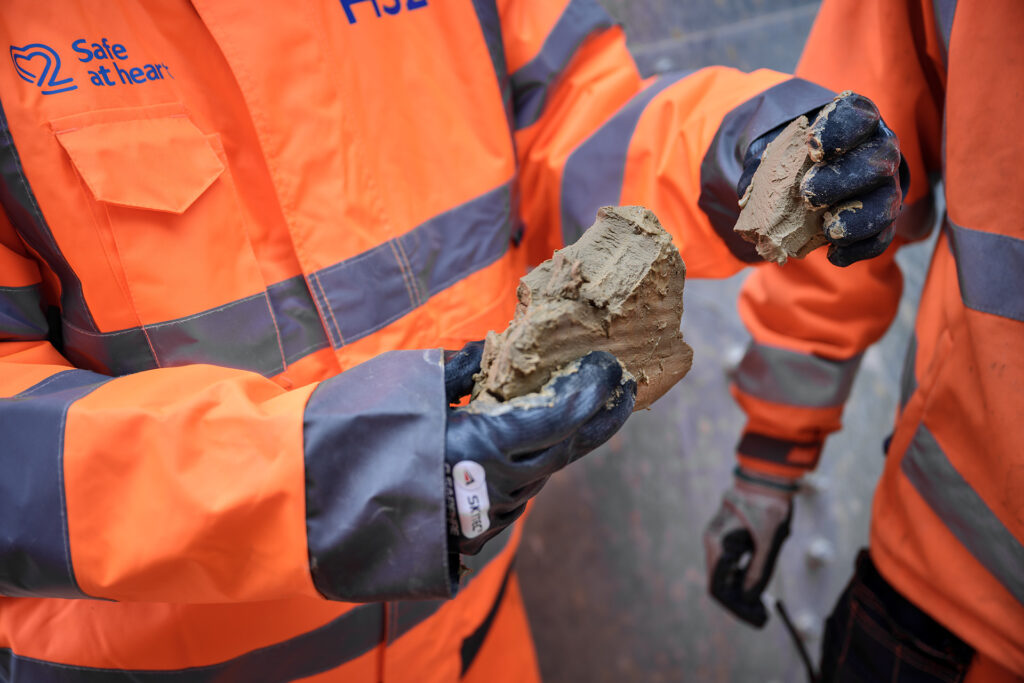
SPEZIALROBOTER
Die Filterpresse entwässert die Feststoffe, die durch den Eindicker aus dem Schmutzwasser extrahiert wurden. Dazu presst sie den Feststoff zwischen vertikalen Platten durch ein Filtertuch. Übrig bleiben dünne, feste „Kuchen“, die in einen darunter liegenden Lagerbereich fallen.
Anschließend werden die Kuchen auf Lkw verladen und in ein nahe gelegenes Gebiet gebracht, das später begrünt wird. Die Filterpresse verfügt über ihren eigenen automatischen Reinigungsroboter, der die Filtertücher mindestens einmal am Tag säubert, um ihre Lebensdauer zu verlängern.
FILTER FÜR DIE FEINARBEIT
Während die Feststoffe zu Kuchen gepresst werden, muss das Wasser im Überlauf des Eindickers drei weitere Filter durchlaufen, um sein Qualitätsziel zu erreichen. Der erste ist ein Koaleszenzfilter, der in einem höher gelegenen Behälter untergebracht ist und die Kohlenwasserstoffe aus dem Wasser herausfiltert. Danach folgen Sand- und Aktivkohlefilter in zwei direkt nebeneinander liegenden Containern.
Vogt zieht die Kunststoffplanen an den Seiten der beiden Container zurück und enthüllt eine Reihe von Tanks, in denen sich die Filtersubstanzen befinden. „Wenn die Anforderung an die verbleibenden Feststoffe weniger als 100 Milligramm pro Liter im Auslauf beträgt, dann brauchen wir die Sand- und Aktivkohlefilter“, erklärt er. „Dieser Sandfilter ist ein spezieller Typ, gefüllt mit verschiedenen Körnungen. Das Wasser fließt von unten nach oben durch die verschiedenen Korngrößen, sodass ein Teil der Schadstoffe im Sand bleibt. Dann durchläuft es nach demselben Prinzip den Aktivkohlefilter.“ Um die Lebensdauer der Filter zu maximieren, spült die Anlage automatisch zurück, wenn der definierte Maximaldruck erreicht ist.
WIEDERVERWENDEN ODER ZURÜCK AUF LOS?
Nachdem das Wasser die Filter durchlaufen hat, wird es in einen kleinen Tank im Inneren des letzten Containers geleitet. Dort messen Sensoren dieselben Parameter wie beim Einlass, um die Effizienz des gesamten Prozesses vergleichbar zu machen. Wie bei mehreren anderen Prozessschritten werden nun Wasserproben entnommen und zur Kalibrierung und Kontrolle getestet. Dies geschieht sowohl an Ort und Stelle als auch in einem externen Labor.
Von hier aus kann das Wasser drei Wege nehmen. Hat es die Qualitätsanforderungen nicht erreicht, wird es automatisch wieder dem Aufbereitungskreislauf zugeführt. Sind die hohen Anforderungen der Umweltbehörde dagegen erfüllt, darf es in das Abwassersystem und den Fluss geleitet werden. Oder das aufbereitete Wasser wird – wie bei diesem Projekt üblich – zurück zu den TBM geleitet und dort kostensparend wiederverwendet. Und so beginnt der ganze Kreislauf von Neuem.
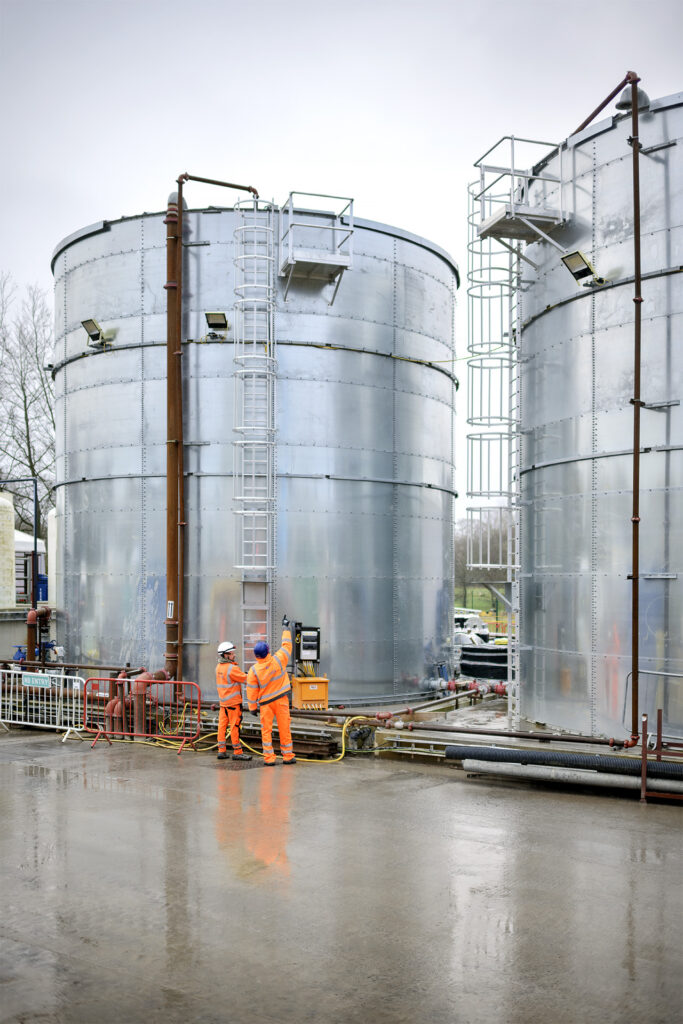
Projektdaten | |
---|---|
Auftraggeber | High Speed 2 Ltd. (HS2) |
Kunde | Skanska Costain Strabag (SCS) JV |
Ort, Land | West Ruislip, London, Großbritannien |
Tunnelvortrieb | seit 2023 |
Anwendung | Eisenbahn |
Geologie | Ton, Kalkstein, Kreide (gemischt) |
Vortriebslänge | ca. 15.757 m |
Maschinendaten | 2x EPB-Schild Durchmesser: 9.829 mm Northolt Tunnel West 2x Wasseraufbereitungsanlage Kapazität: 150 m³/h 1x Kühlanlage 1x Dosieranlage |