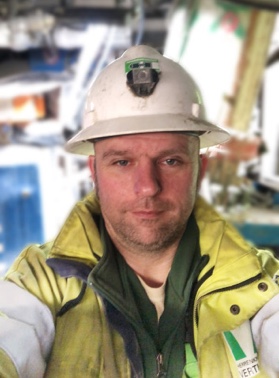
On the sprawling site of the Nezhinsky mine in Lyuban, Belarus – about a two hour drive south of Minsk – Marcus Winterer climbs into a metal manrider. In the past two years it has taken him vertically underground on countless occasions. Winterer is one of the supervisors for two innovative Shaft Boring Roadheaders (SBR) from Herrenknecht. These two high-tech giants sank two shafts here in record time, 697 and 750 meters deep and 8 meters in diameter. As the 2,300kW hoist starts with a clear signal, Marcus Winterer descends into the depths at 8 meters per second.
Through the perforated sheeting of the manrider the Herrenknecht specialist sees the walls of the lined shaft rushing past. “I’m proud of what we’ve done here,” says Winterer. “It was a challenge for us and our partners. We have achieved revolutionary progress together.” Then he reaches the bottom of the shaft, above which the SBR’s mighty cutting drum currently stands idle in the potash horizon – for the first time in two years.
Since construction began in 2018, supervisor Winterer has been responsible for ensuring that the shaft sinkers from Redpath Deilmann GmbH in Dortmund were able to operate on the Belarusian jobsite at high performance without interruption, around the clock, seven days a week. To do this, he trained personnel, coordinated with electricians and mechanics and created maintenance plans.
„The 21st century of mining“
The deployment of the SBR was a pioneering underground mission from the start. Commodity producer Slavkaliy wants to mine the deep deposits of reddish shimmering potassium salt. With the new method, the company wanted to develop the new mine as quickly and safely as possible. The coveted commodity is mainly used in agriculture as a fertilizer. The Belarusian commodity company expects a yield of 2.2 million tonnes per year. For this, around 7 million tonnes of potash ore have to be mined and removed.
In the summer of 2016, multinational businessman and IOOO Slavkaliy founder Mikhail Gutseriev and entrepreneur Martin Herrenknecht directly came to an agreement in Schwanau. With a handshake, they agreed to tackle this ambitiously planned shaft sinking mission with the latest technology. The specific order was that in 12 months Herrenknecht was to design and build two huge, innovative SBRs for the mechanized sinking of the service and production shafts down to the potash deposits. The businessman Gutseriev also made clear publicly what he expects from the project: “Our approach is the 21st century of mining!” The words were followed by tangible pioneering actions.
The successfully completed project marks a boost to innovation that resounds in the industry. In addition to innovative shaft boring technology, the constructive teamwork of the partners involved in building the shafts contributed to this success.
In July 2017 the Dortmund-based mining company Redpath Deilmann GmbH – formerly Deilmann Haniel – was awarded a contract by IOOO Slavkaliy to develop the underground mineral deposits with the mechanized Shaft Boring Roadheaders from Herrenknecht AG. Redpath Deilmann would then also excavate around 10 kilometers of underground routes and a loading bunker.
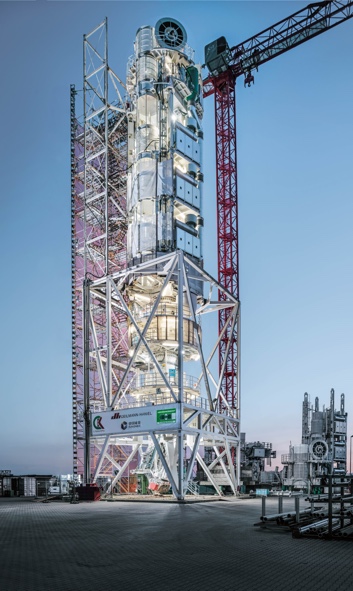
Summer 2018: workshop acceptance in Schwanau by Redpath Deilmann for the two Herrenknecht Shaft Boring Roadheaders
„Mining as a whole is not an individual business. It’s pure teamwork. You have to be able to trust each other blindly.“
Michael Niermann,
General site manager Redpath Deilmann GmbH
Boosting performance continiously
The time scale for the mechanized construction of the two shafts at the Nezhinsky mine represents an particularly ambitious benchmark: compared to construction progress in soft and medium-hard rock with conventional methods, both SBRs were to reach the final depths of 697 and 750 meters twice as fast. In other words: the shafts descend into the depths twice as quickly as is usually the case using blasting techniques.
Nothing was left to chance in the interaction of Herrenknecht machine technology, the shaft construction planning and shaft design of Redpath Deilmann and the specifications of project owner Slavkaliy.
In June and August 2018, Redpath Deilmann formally accepted the two huge, fully assembled machines at Herrenknecht’s headquarters in Schwanau, which rose like towers to a height of 45 meters. Around six months later in December 2018 and January 2019 the SBR cutting drums were eating into the Belarusian soil for the first time. That alone was a remarkable achievement, because a completely new team of shaft sinkers, machine manufacturer and commodity producer using a completely new type of mining technology had to start sinking the shafts in a relatively short time. Thanks to perfectly organized work preparation and planning, the signs were good for sinking the shafts in record time.
In April 2019, Shaft 2 had already reached a depth of 165 meters. Throughout the project, with concentrated and cooperative collaboration the partners managed to continuously improve performance.
144 meters of top performance
Michael Niermann, chief site manager at Redpath Deilmann, has 37 years of shaft sinking experience. Projects all over the world bear his signature. The advantages of the new technology are obvious to him: “Normally, separate work steps follow one another: you drill blast holes, blast, ventilate, muck out and then the shaft wall is lined and secured,” he explains. “With the SBR, the process is fluid, mucking and lining work take place at the same time.” The dangerous work with explosives is no longer necessary thanks to the mechanized excavation – and higher performance is also possible.
A pioneering project record was then set in April 2020. On social media channels the sinking crew proudly announced a top performance of 144 meters of shaft in one month, with a peak performance of 7.4 meters of advance per day. At Redpath Deilmann, which can look back on 132 years of proud mining history, it broke an internal company record set in 1938 – which was achieved at the time thanks to practically non-existent safety regulations.
The shared successes welded the miners from Belarus, Russia, Ukraine and Germany together. “Everyone was enthusiastic about the technology and highly motivated to drive it forward,” says Niermann. “We got together every day and pushed each other. At first we optimized ourselves by hours, later by minutes and toward the end it was a matter of saving seconds.”
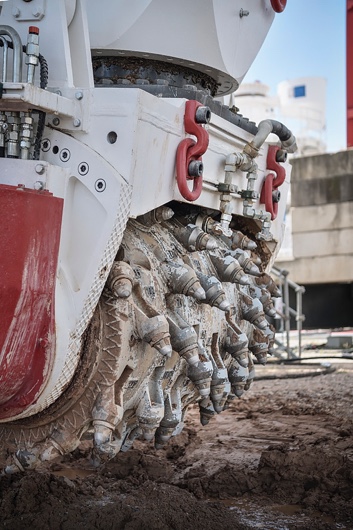
„I had never experienced anything like this in my career up to that time. The enthusiasm of our crews when the machine was in the shaft and started operations.“
Jochen Greinacher,
CEO Redpath Deilmann GmbH
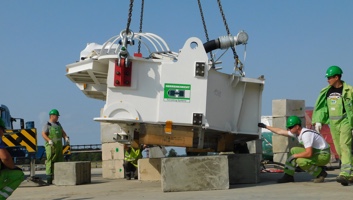
Schwanau to start of excavation in Belarus
A look at the sinking records of conventional methods puts the progress achieved in the Nezhinsky project into perspective: with drilling jumbos and blasting, 1 to 1.5 meters of shaft are created daily. With the two new shafts in Belarus, an average rate of more than 3 meters per day was achieved. Shafts 1 and 2 were built in 17 months of active excavation.
This speed is a worldwide industry first, coupled with high safety requirements for the miners involved in shaft construction. “Usually we make progress of one to one and a half meters of depth a day. Here we managed over five meters a day in the final month of excavation.” Niermann is convinced that the SBR will establish itself worldwide.
On July 17, at 697.1 meters the second Herrenknecht SBR reached its final target depth in Shaft 2. Not a single reportable industrial accident had occurred since shaft sinking operations began. Together with his colleagues from Slavkaliy and Redpath Deilmann, Marcus Winterer celebrated the arrival of the last muck kibble on the surface that day. A real milestone in the history of mechanized shaft construction, which not only had the miners on site cheering. “This project has welded us together as a team from the start. We will now disassemble the two machines – and to be honest, it will also be a little sad,” says Herrenknecht specialist Winterer toward the end of the pioneering project in Belarus.
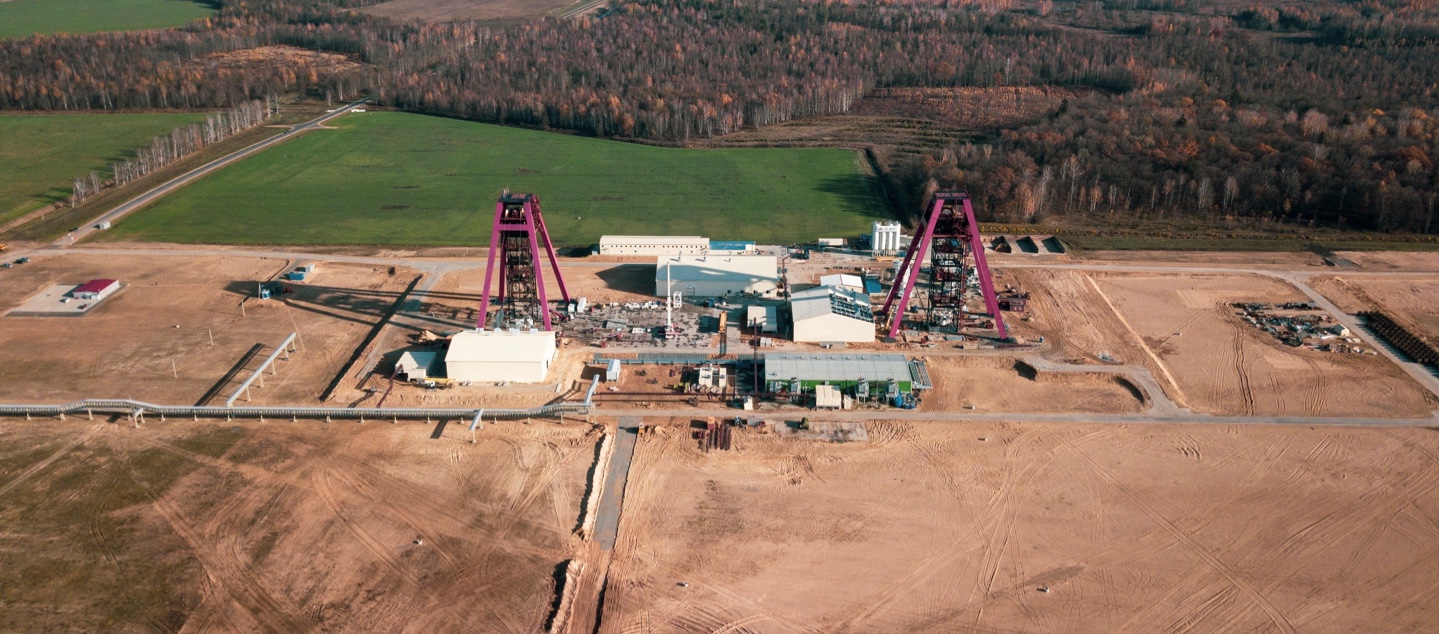

Redpath Deilmann GmbH is a long-established and globally renowned player in the mining business that has always focused on innovation: for over 130 years the company has shaped the industry and been involved in numerous pioneering developments.
- Founded in 1888 as C. Deilmann AG
- In addition to Dortmund, Germany, other company locations in Russia, Belarus and Serbia
- A Redpath Group company (Redpath Mining Inc., North Bay, Canada)
- Number of employees: around 900 in Germany, Russia and Belarus
- More than 560 shafts with a total depth of 235 km built worldwide
Developing proven technology further
The SBR technology has its origins in a method that has been tried and tested for over 15 years: the mechanized Vertical Shaft Sinking Machines (VSM) from Herrenknecht for launch or reception shafts in utility tunnelling with a comparatively shallow depth of up to around 150 meters. Herrenknecht comprehensively developed this method further for the specific requirements of mining.
For mining the SBR is equipped with a boom that can be swiveled through 360 degrees and a hydraulically driven rotating cutting drum. A newly developed pneumatic system transports the soil removed from the bottom of the shaft. The elaborate work decks are also adapted to the complex work and logistics processes of the underground mission.
The hydraulically driven SBR roadheader is telescopic. The desired shaft cross-section can thus be adapted if necessary – without costly retrofitting. “It was a great feeling when everything was working well and the very first bucket of muck came to the surface,” Winterer recalls.
The SBR achieves optimal results when, at an early stage in the planning, mine operators and shaft builders design the shaft to meet the specific requirements of the technology. “The machine is the heart of a complex system in which all the little cogs need to mesh together,” says Frank Otten, Vice President International Projects at Redpath Deilmann. As division manager he installed a qualified team on site that set up and operated the complete supply and debris clearance of the machines as well as all surface facilities.
Due to a water-bearing layer of earth, the ground was frozen to a depth of 165 meters. A breach with a water ingress at the end of the freezing depth then turned into the greatest challenge in the project for Otten: “No matter how good the preparations are, not everything goes to plan underground. Ten percent uncertainty remains – it just always depends on how you deal with it.” The partnership withstood the challenges: Slavkaliy, Herrenknecht and Redpath Deilmann always managed to make consensus decisions and quickly agreed on efficient safety measures in the difficult geology.
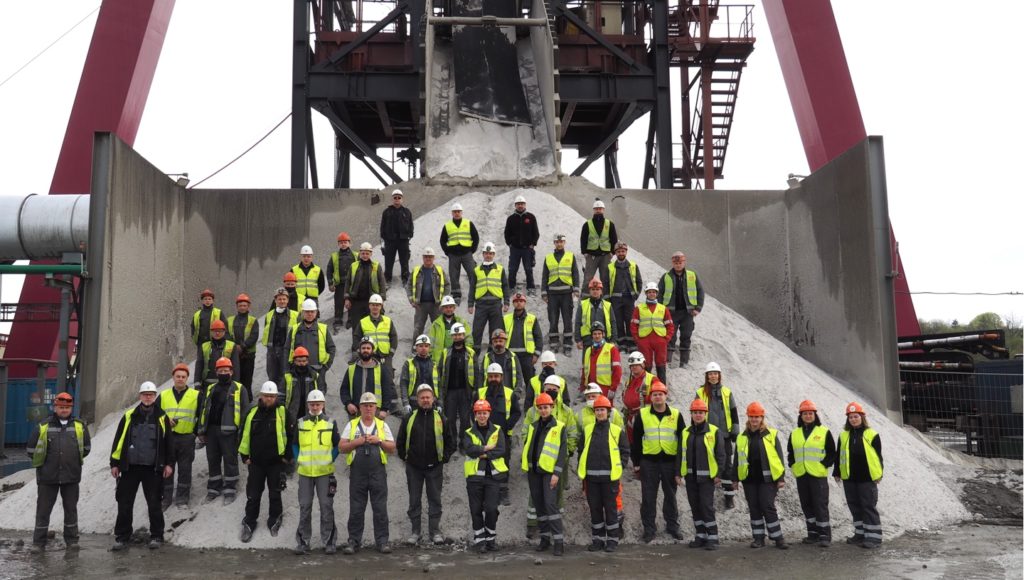
The racing bike for the Tour de France
For Patrick Rennkamp, the collegial interaction of all those involved was also a decisive key to the success of the project. As Product Manager at Herrenknecht, he dedicated much of his professional life to the evolution of the SBR. From almost ten years of development work to the initial deployment with DMC Mining Services in the Jansen Mine in western Canada to the groundbreaking performance promise and the baptism of fire in Belarus. The experience gained is engraved in the machine’s DNA: “It’s as if we invented the bicycle with DMC Mining Services and then developed the racing bike with Redpath Deilmann that wins the Tour de France,” says Rennkamp.
Together Herrenknecht and Redpath Deilmann evaluated the results of the reference project in Canada. The Herrenknecht engineers then optimized the pneumatic mucking system, which removes the muck from the bottom of the shaft into a suction tank. In addition, the sheaves for the support ropes, for example, were relocated, which enabled larger components to be installed on the decks. “Communication between the companies was constructive and results-oriented at all levels,” says Rennkamp, who is visibly pleased by the successful achievements. This is another reason the site crew was able to start excavation in Belarus just six months after factory acceptance in Schwanau.
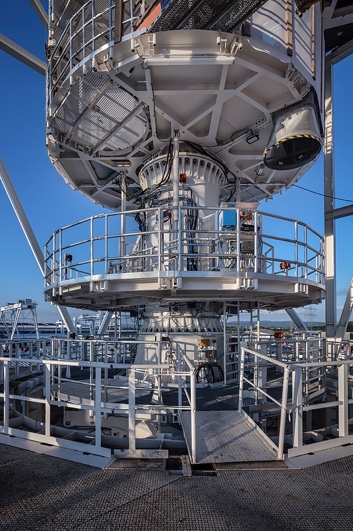
Close up of one of the SBR working decks
„People’s safety comes first.“
Martin-Devid Herrenknecht,
General Manager Mining
Martin-Devid Herrenknecht, General Manager Mining, sees in the project the roots of a future-oriented collaboration between Herrenknecht and Redpath Deilmann. “Our partners understood the technology exactly and set up the logistics and operations masterfully,” says Herrenknecht. “This was particularly evident in the critical interfaces between our machine and the technology specific to shaft construction.”
“Conventional mining projects are often completed years late due to practical limitations and unexpected complications,” says Herrenknecht. “To beat the deadline as in Belarus is extremely unusual.” The starting point for everything was the bold and forward-looking decision of IOOO Slavkaliy to use the modern technology from Herrenknecht and commission Redpath Deilmann with the execution.
Satisfy the hunger for innovation
Jochen Greinacher, CEO of Redpath Deilmann, is not surprised that shaft construction methods are now also making a leap in development. Instead he had wondered when it would finally happen. “The whole mining world is looking at our project in Belarus and is extremely hungry for innovation. I’m certain this technology will change our industry, “says Greinacher. He is glad that Herrenknecht pushed the development forward and that Slavkaliy had the courage and the foresight to use it: “In the end, the SBR worked better than I had expected – and even dared to hope. We could only achieve this – as well as being accident-free – with a really seamless team on site, in which everyone involved in the project worked toward the same goal.” Once again, his company will be at the forefront when a new era of mining is ushered in.
Slavkaliy Nezhinsky Mine Project | |
---|---|
Client | IOOO Slavkaliy |
Contractor | Redpath Deilmann GmbH |
Location | Lyuban, Belarus |
Machine data | 2x Shaft Boring Roadheader |
Diameter | 8 m |
Depth | Shaft 1: 750 m Shaft 2: 697 m |